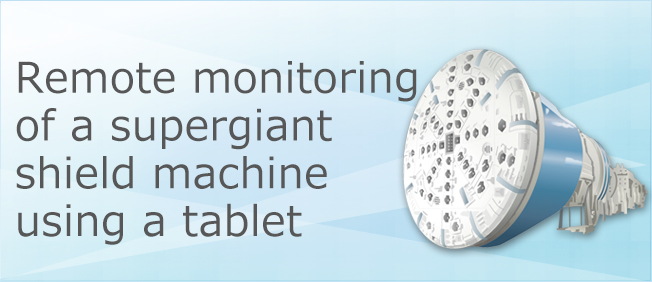
Meet the shield machine electrical designer who's responsible for introducing Pro-face Remote HMI remote monitoring software from Pro-face at a manufacturer handling everything from development and production to sales of construction and mining equipment and hydraulic machinery. As an electrical designer, keeping up to date with the latest technology is a must, making Pro-face Remote HMI an ideal tool. This section introduces the benefits of using a tablet for remote monitoring of tunnel drilling equipment.
Using remote monitoring to check the tunneling machine status from a location kilometers away
Normally, the only way to know the status of a shield machine is to be in the operator's cab. In order to check the progress of the shield machine and the tunnel mining, you'd need to make a trip to the control room. With smaller shield machines, the distance between the operator's cab and the drilling equipment is short, so time isn't too much of an issue. With larger mining equipment, however, the overall size of the device can exceed 100 meters. Also, as the tunnel grows, the distance from the control room also grows. This translates to more effort and even more time when checking the device status from an aboveground office at the construction site.
With Pro-face Remote HMI, it's possible to remotely monitor the shield machine, allowing the progress to be checked without having to go into the tunnel and all the way to the operator's cab. Moreover, multiple non-operator supervisors and others managing the progress are able to check the status of the equipment remotely and simultaneously. And if while checking the status of the shield machine it seems that a problem is likely to occur, Pro-face Remote HMI makes it possible to take appropriate countermeasures in advance, reducing the likelihood of trouble occurring. Even if a problem does occur, it's possible to proceed with the tunnel mining project without a delay in the construction schedule, which is sure to make construction contractors happy.
Checking the shield machine status from multiple tablets from any location
With Pro-face's GP4000 Series HMI attached to equipment, it's possible to collect information by communicating with devices using a variety of extensive protocols. This means that, using HMI, it's possible to ascertain such information as the torque and speed of shield machine's cutter and the temperature of various devices. Using HMI and Wi-Fi together, it's possible to access this information to understand the status of the shield machine remotely using multiple tablets. And because the information can be displayed on a tablet, the status can be ascertained from anywhere, be it inside the tunnel, outside the operator's cab, or in an on-site office.
Checking tunnel excavation equipment in real time without stopping work
With asynchronous mode, you are able to use the tablet to see not only the operating screen but also other screens. Because it's normally possible for shield machine technicians inside the tunnel to check screens other than the operating screen, they are able to avoid troubles in advance by taking countermeasures, thus reducing the likelihood of maintenance and other trouble. Compared with products from other companies, Pro-face Remote HMI boasts faster response times and the ability to monitor screens the operator doesn't usually see. This is one benefit electrical designers of shield machines often praise.
Reliability of genuine brand software
Because the dedicated application is offered by the manufacturer, it offers enhanced stability, improved reliability, and functional aspects compared with other remote desktop applications. Also, with continuous updates expected in the future, you can anticipate continued superior usability.
Testimonial from the supervisor
Easy real-time remote monitoring
After seeing the demo, I wanted to start using Pro-face Remote HMI right away. We are always looking to incorporate new technology, and with the response speed and ease of installation, we were happy to find this product. As an equipment manufacturer, we are always looking to solve problems before they occur, and wherever we put this product to use it seems there are fewer troubles, increasing the reliability of the equipment itself. Because fewer problems occur, there's less worry about falling behind the construction schedule, which is pleasing to the construction company. And by taking advantage of on-site Wi-Fi, there's no need for wiring work, making introduction simple. Also, because it's possible to perform checks via the Internet, technicians are able to solve problems without ever having to go to the site, which is a system that seems to benefit everyone. Setting up win-win scenarios is usually quite difficult, but using this application and a tablet, it was easy to accomplish.