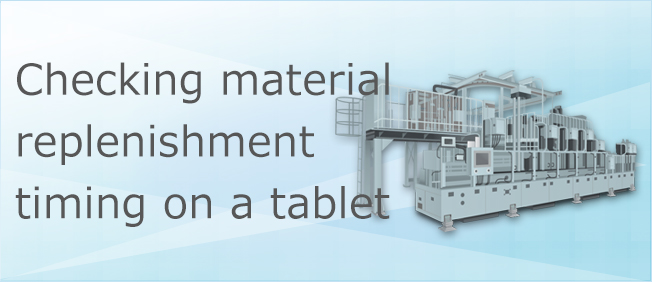
This section introduces a manufacturer of toner cartridges for printers. Traditionally, checking remaining amounts in toner cartridge filling lines has proven to be a very inefficient operation, and finding a way to improve the operation has been a challenge. Let's look at how this factory has used Pro-face Remote HMI remote monitoring software to improve efficiency.
Checking legularly remaining amounts can be wasteful and inefficient as well as carries with it a risk of running out of materials.
Toner cartridges use four colors, cyan, magenta, yellow, and black (CMYK). In this factory, four toner-filling devices are placed at 10-meter intervals. Operators check the remaining amount of toner inside the tanks, and if they need to be filled, the operators must bring more toner.
However, the daily production amount fluctuates for each color, and the speed at which the material is used up varies. This is why operators must regularly check on the four devices, to constantly be aware of how much any given color has decreased (usually about five patrols each day).
For this reason, checking remaining amounts is more than just time-consuming and inefficient. It also carries the risk of one wrong step causing the toner cartridge material to run out, stopping the entire line.
Check remaining amounts of ink with a tablet. Increase work efficiency by predicting future needs.
At this toner cartridge manufacturing site, display panels are installed on the toner filling equipment to show real-time remaining amounts for raw materials. Being able to check the information displayed on those panels from anywhere means operators are able to optimize their movements for maximum efficiency.
That's what led this toner cartridge manufacturer to consider introducing Pro-face Remote HMI remote monitoring software. By carrying around a tablet with this application installed, operators are able to check the information on any device from anywhere when they need to check remaining amounts.
Operators can look at a tablet and think, "It's nearly time to fill the cyan, and the magenta is getting close, so I might as well prepare both." In this way, operators can predict situations before they happen and keep on top of material replenishment, thus improving overall manufacturing productivity.
The ease of introduction and the high degree of freedom compared with "Andon displays" are appealing.
In addition to setting up remote monitoring using Pro-face Remote HMI, this toner cartridge manufacturer also considered connecting "Andon displays" to its PCs.
"Andon displays" requires a large LCD monitor to be installed on-site, which means they would have needed somewhere to install the equipment and somewhere to route the wiring. In addition, checking the remaining amounts in the various locations would have required installation of multiple units. This proved to be too high a hurdle for a factory already in operation.
On the other hand, because Pro-face Remote HMI only requires a Wi-Fi router to be installed with no need to worry about factory layout, setup is easy. With that in mind, the manufacturer chose to go with Pro-face Remote HMI.
Enhanced cooperation with following steps through efficient collection and distribution of production data.
Along with Pro-face Remote HMI, the manufacturer also installed Pro-Server EX data management software.
Pro-Server EX is data management software that collects data such as production statuses in a PC in real time. It is also capable of delivering production planning data such as recipes. By installing this software, not only personnel for managing downstream steps can check the operation status of the toner filling line and prepare accordingly, but those in charge of the factory are also able to ascertain the overall manufacturing status from office areas.
In other words, the manufacturer made it possible not only for operators to see the status of the toner cartridge line, but for people in various positions to ascertain the status as well.
Testimonial from the supervisor
It was surprising how easy it was to connect to our existing equipment.
Performing regular rounds inevitably leads to wasted actions by operators, so we wanted to improve the situation. There are numerous products from every company when it comes to remote monitoring systems, and thinking about setup and costs for installation really kept us from moving forward. With Pro-face Remote HMI, however, setup was really simple. Getting the system up and running required no special programs, and we were able to use our existing GP4000 Series devices with only a few changes to settings. We were able to go wireless just by setting up an average tablet device and a wireless router. If we had known setup would be this easy, we would have done it a long time ago.